A new ready-for-assembly track-lighting system showcases Kurt Die Casting’s complete-part capabilities.
The system includes three parts: a heat sink, pivot bracket and yoke arm die cast from A380 aluminum alloy. These capabilities are coming at a time when lighting companies need complete parts.
The lighting industry has been hit hard by offshore labor costs and shipping delays. To reduce cost and transportation issues, a large producer of commercial and consumer lighting approached Kurt as an alternative domestic supplier. The assembly the producer needed was for a large retail chain with several stores and the demand was high. They came to Kurt seeking engineering help that required print-to-production capabilities. They needed to be confident that when they handed off a set of complicated drawings to a manufacturer, they’d receive ready-to-assemble parts.
“A program like this is a good fit for our Die Cast Division. We offer customers the best value when we can manage the full part program”
Chuck Remillard, Vice President of Contract Sales
The primary die casting process started with four-cavity molds and trim die. Secondary operations included turning, machining, sanding, sand blasting and painting. These parts require extreme attention to detail with a refined finish on all visible surfaces. Kurt developed casting, handling and paint processes that rival offshore labor and quality to meet these standards. Kurt also worked with specialized process suppliers for chemical coatings, paint and packaging to ensure the utmost quality.
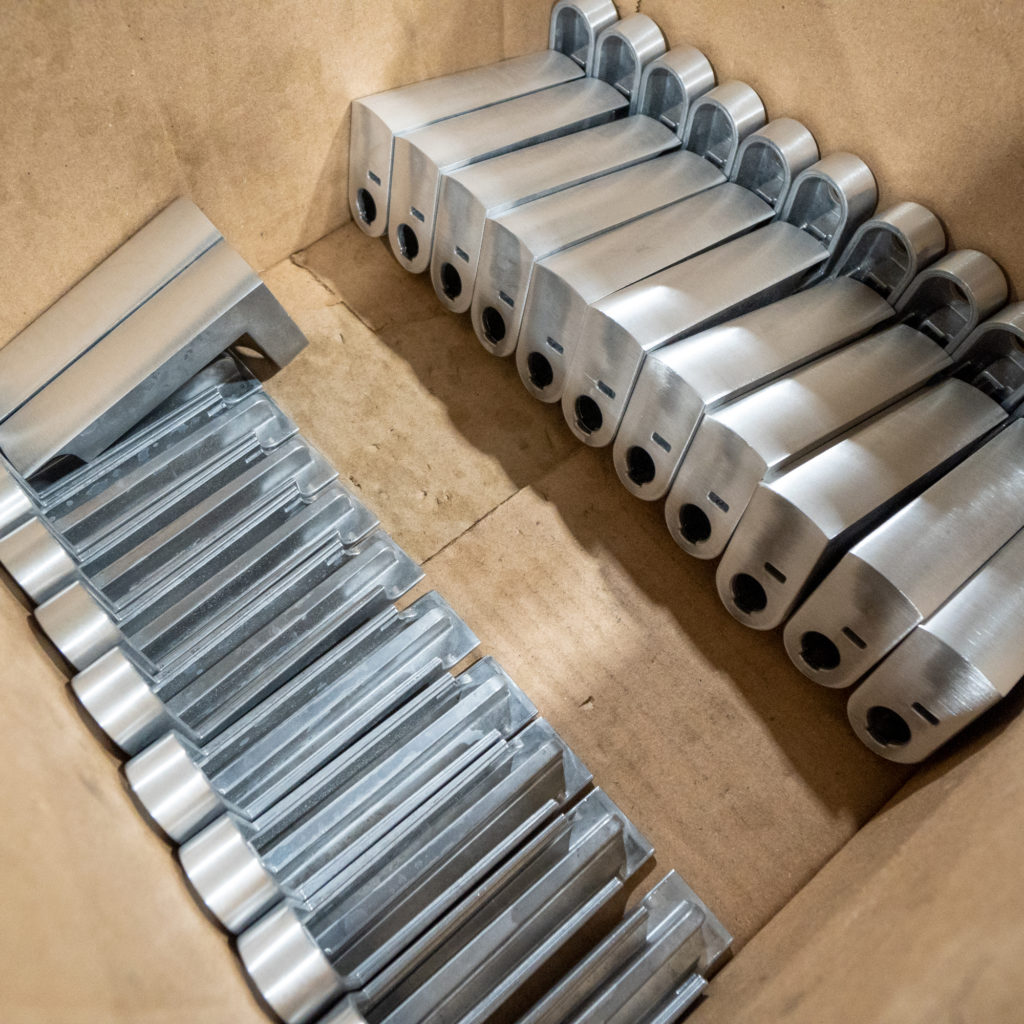
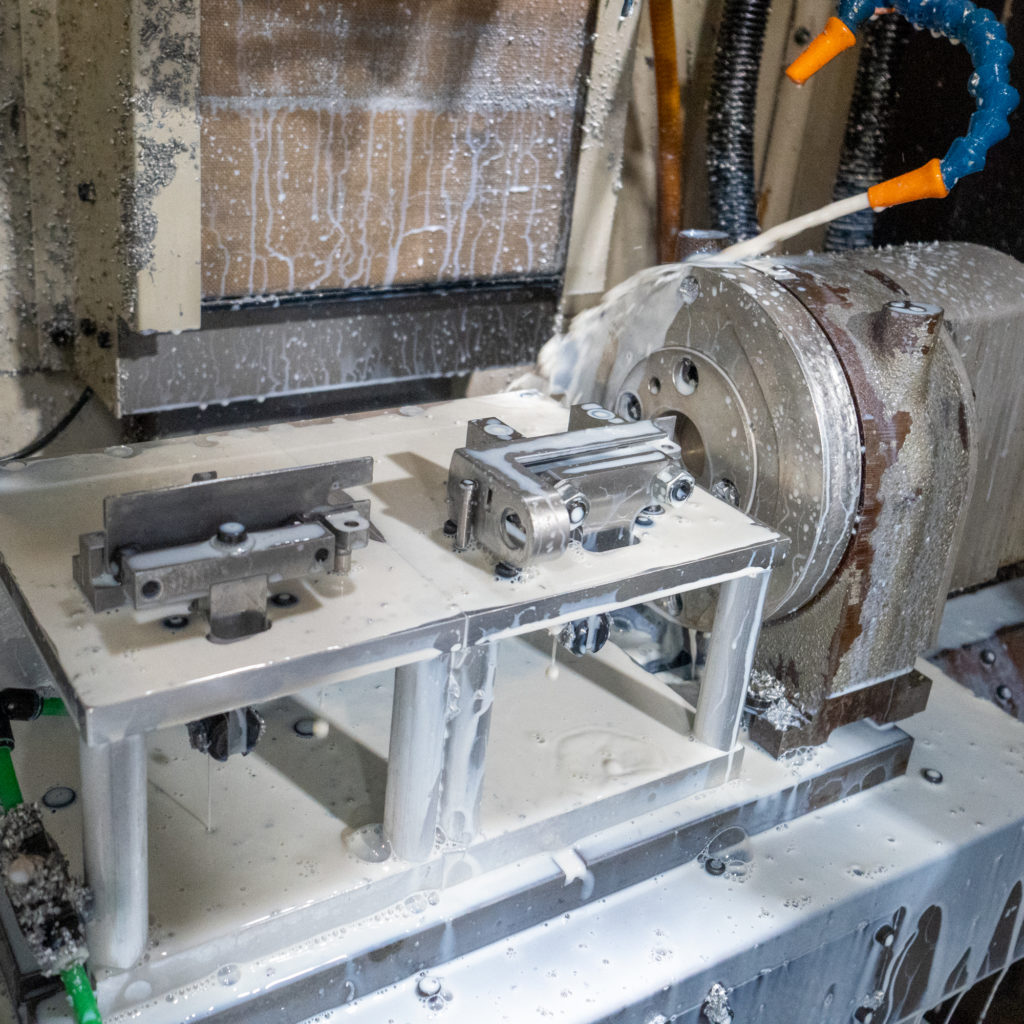
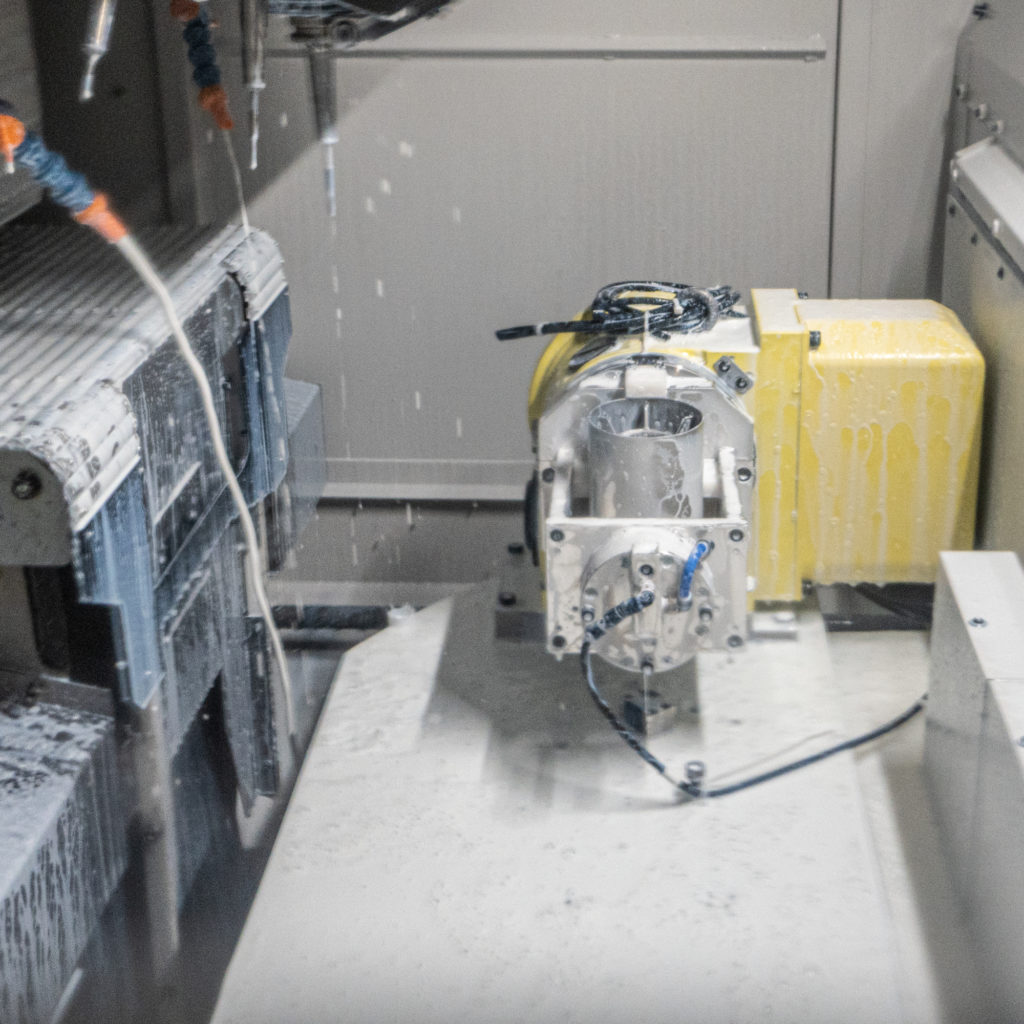
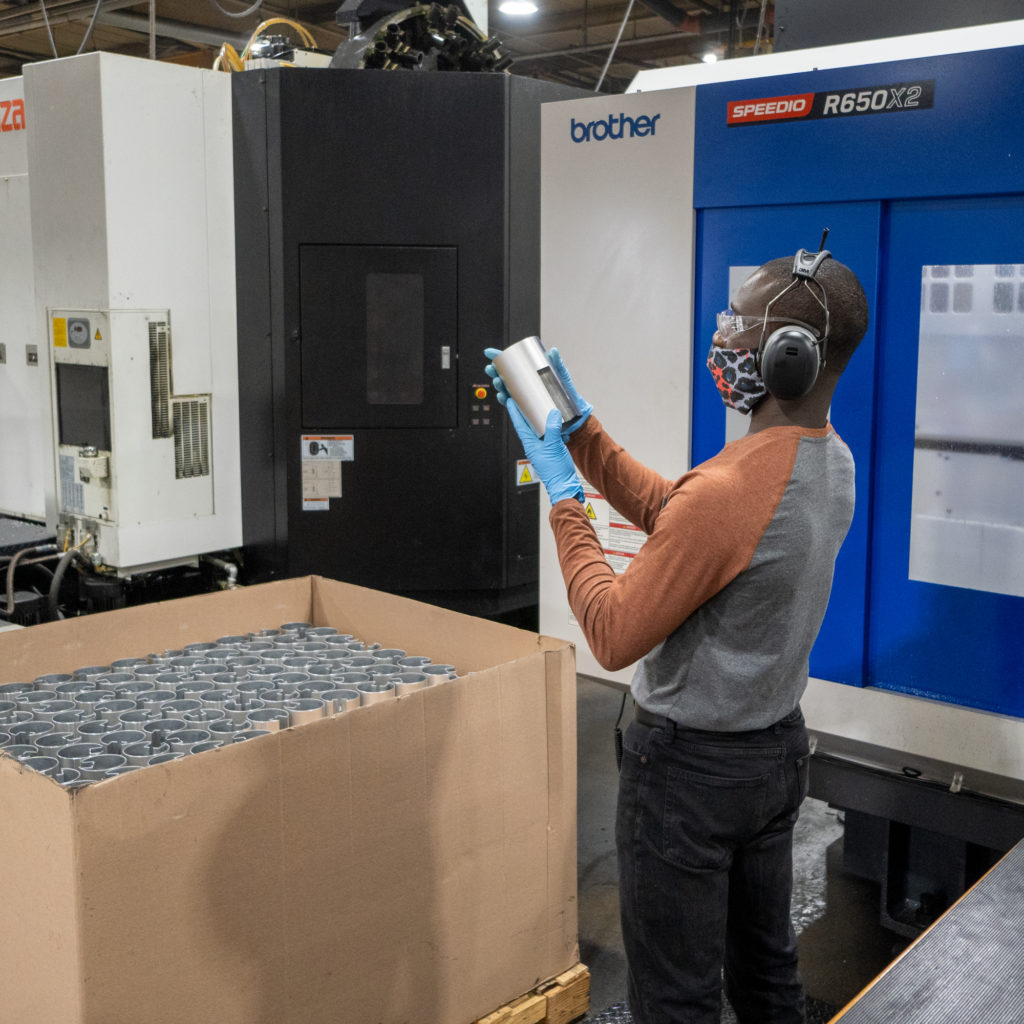
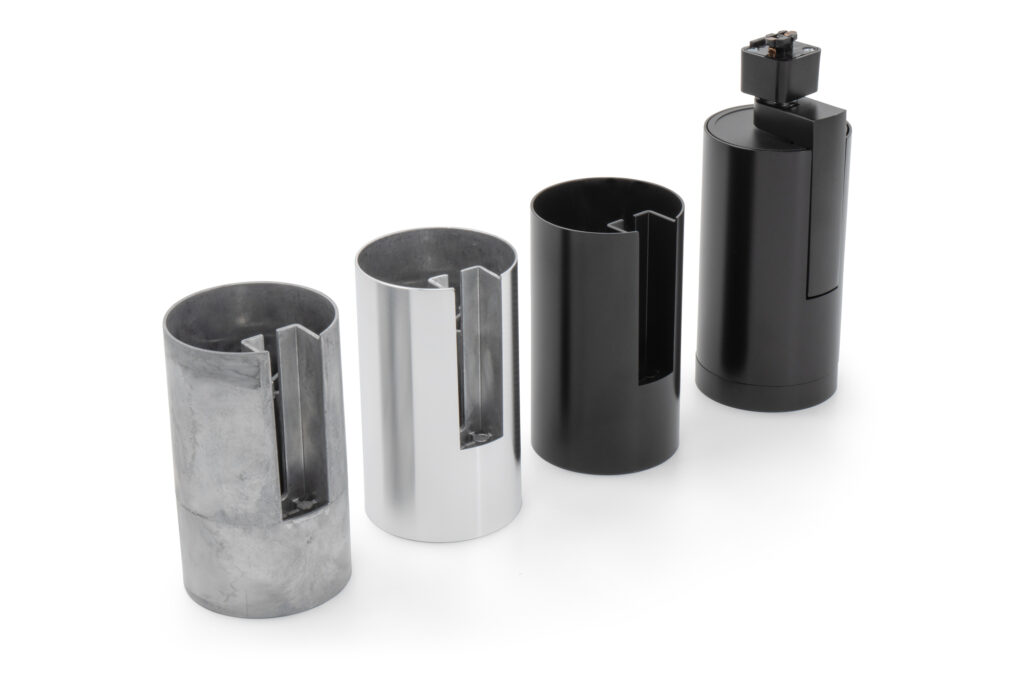
Technical Specifications
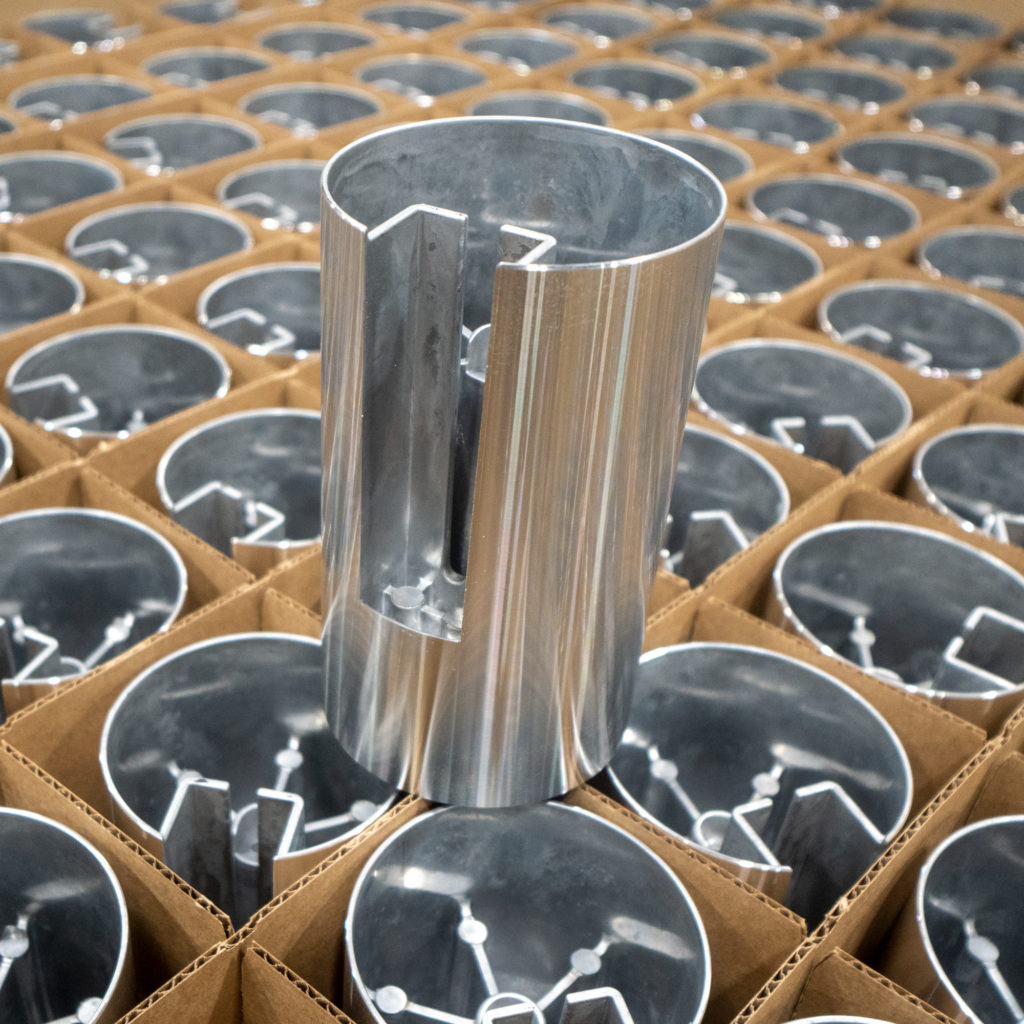
- Part Size Range: Up to 5” x 6”
- Weight: .50 lbs. to 3 lbs.
- Material: A380 aluminum
- Molds: 4 Cavity
- Assembly Pcs: 3
- Secondary operations: Turning, Sand Blasting, Machining, Hand Buffing, and Paint
- Part Quantities: 100,000+ EAU
- Quality Requirement: Strict Cosmetic Requirements
- Automation: Automated ladling and part extraction
- Machine Tonnage: 600-900 Ton
Kurt managed all aspects of production including tool design for maximum die-casting efficiency and cost savings. Other savings opportunities benefited the customer when Kurt incorporated automation, secondary operations and packaging into the program. Automation plays an important role in each part produced at Kurt’s Fridley, MN, facility helping to reduce overall costs for the customer and ensuring consistent die-cast part quality.
“This program highlights what we can do from start to finish using our total-team capabilities at Kurt Die Casting,” said Chuck Remillard. “It included tool design, primary die casting operations and in-house machining and finishing. Program work is what we do best for the customer.”Kurt worked hard to capture the business by offering strong engineering support, material management and a ship-to-stock logistics program. Kurt has top program management services along with Die Cast capacity, secondary machining, and Quality.