This month we’re putting the spotlight on a new industrial LED lighting heat sink in production at Kurt Die Casting. Please check out the video and read up on the processes and improvements we brought to this new part.
A large industrial light manufacturer approached Kurt Die Casting with a request for a quote on a large LED light heatsink for a commercial application. Due to supply chain delays and cost, they decided this should be a program manufactured in the USA. They contacted Kurt to help with re-tooling, better pricing, and improving the design. They were faced with several issues that needed to be solved. The first was a tooling problem. They had a die that was degrading quickly and getting fewer parts than expected, driving up costs and slowing production. The second issue was inventory management. The customer had part-demand peaks and valleys and wanted to order parts weekly from a supplier without warehousing the inventory themselves.
Die Casting Part Spotlight
This month we’re putting the spotlight on a new commercial LED lighting heat sink in production at Kurt Die Casting. Please check out the video and read up on the processes and improvements we brought to this new part.
“We integrate technology throughout our processes in our major program jobs. Using Kanban inventory management is a huge customer benefit. It’s a pull system designed to reduce a customer’s on-hand inventory by shipping materials as needed. When inventory analysis indicates that stock is depleted, the customer notifies us via email, and we ship out the parts from our inventory.”
CHUCK REMILLARD, VICE PRESIDENT OF KURT MANUFACTURING CONTRACT SALES
The job requirements included primary large-part die casting on a 9-pound finished part, program management, tool design and production, secondary machining operations, inventory management, and installation-ready shipped parts. Final part requirements included tight tolerance machining and cosmetic finishes.
“This job really matched our end-to-end capabilities since it started with creating better tooling and finished with inventory management,” said Chuck Remillard, Vice President of Kurt Manufacturing Contract Sales. “Our engineers used extensive computer mold-flow analysis to design a tool with a 30% increase in tool-life expectancy over the customer’s previous tool—with savings passed on to the customer. We also put our Kanban inventory system into play with on-demand weekly deliveries to meet production needs for exactly the right number of parts.”
The heat sink is cast from A360 aluminum alloy for superior heat dissipation. Each part requires primary die casting and secondary machining operations. Parts are cast with a 1-cavity mold, designed by Kurt engineers using mold-flow analysis and premium materials to reduce wear. Finished parts can be found in applications ranging from warehouse lighting to outdoor and industrial.
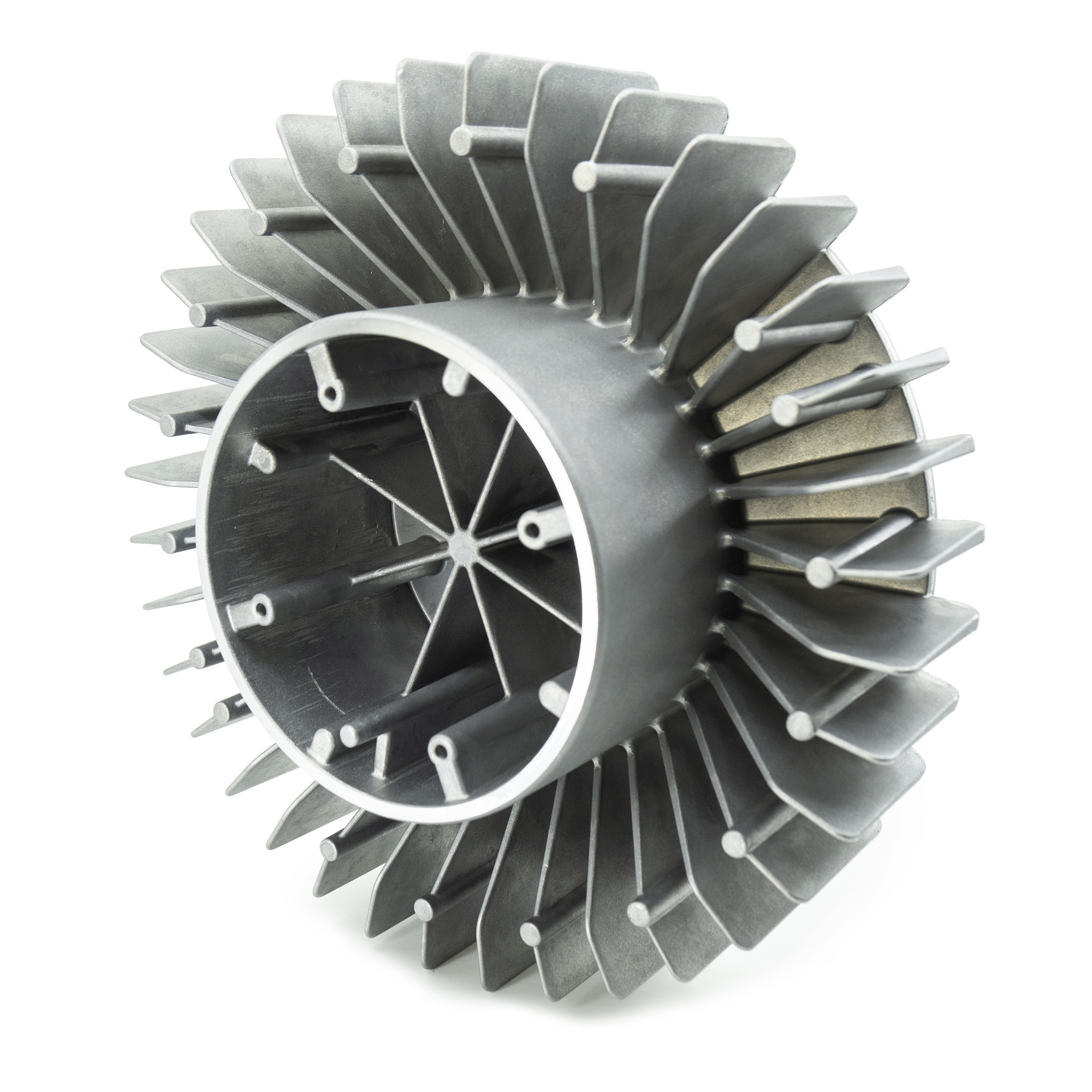
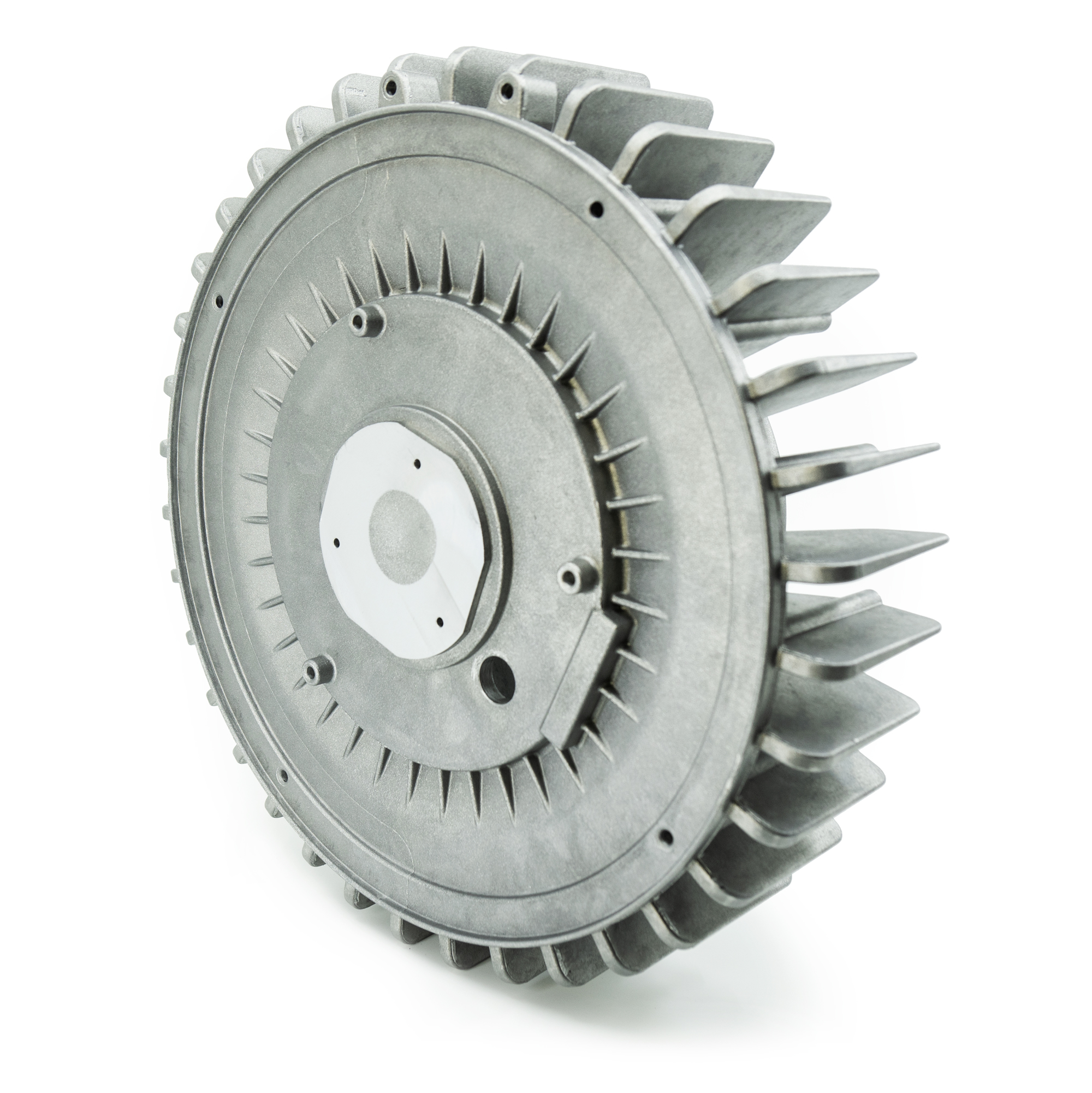
The production process is straightforward: A360 aluminum alloy is robot-ladled into a Buhler 800 Ton Die Cast Press, and the part is formed. A Fanuc robot unloads each 12 x 4-inch part from the die cast press and dunks it in a quenching tank before placing it on a conveyor. The operator trims the casting and boxes the parts. Similar systems are in place throughout Kurt Die Casting, facilitating lean operation and improving employee safety and production efficiency.
Next, the parts are moved to a Doosan 4-axis Horizontal CNC Machining Center, where they are machined, drilled, and tapped before getting quality checked and entered in our Kanban Inventory System for on-demand shipping.
“We integrate technology throughout our processes in our major program jobs,” said Remillard. “Using Kanban inventory management is a huge customer benefit. It’s a pull system designed to reduce a customer’s on-hand inventory by shipping materials as needed. When inventory analysis indicates that stock is depleted, the customer notifies us via email, and we ship out the parts from our inventory.”
With comprehensive program management, in-house machining, engineering support, and tool design, Kurt Die Casting should be your first stop when sourcing a program or part.
Lighting Heat Sink Technical Specs:
- A360 aluminum
- Single cavity mold
- Weight: 9.0 pounds
- Size: 12 inches by 4 inches
- Secondary operations
- Machining
- Quality Requirement
- All parts are considered highly visible. Part defects are unacceptable and must be held in accordance with the part print.
- Automation
- Fanuc robot
- All die casting work centers feature automated ladling and part extraction
- Die Cast Machine: Buhler 800-Ton
Interested in learning more about Kurt die casting or complete part capabilities?
Connect with us today: request a quote or sales@kurt.com